機械加工の仕事をしていると何かとメンテナンスを面倒になるでしょう。
僕自身が実際にメンテナンスをした事により、助かった成功事例を紹介します。
機械加工初心者の人は是非参考にして、日々の生産に役に立てて下さい。
関連リンク
日常的にメンテナンス実施した成功例
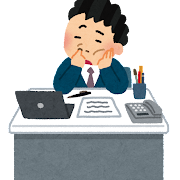
生産優先にしていると何かと怠りがちなメンテナンス。
メンテナンスは本当に面倒ですね、大体の人はこのように考えます。
- 生産止めてまでやる事なの
- 面倒だからやった事にしておこう
- メンテナンスの必要性が感じない
メンテナンスを怠る人の気持ちはこんな感じでしょうか。
僕も機械メンテナンスは面倒です。
その他にも安全に対する意識のメンテナンスもあります。
今ではやっといてよかったという気持ちが上回りますね。
それでは僕が実際メンテナンスしてよかった成功例を紹介します。
日常的に実施した旋盤のメンテナンス事例
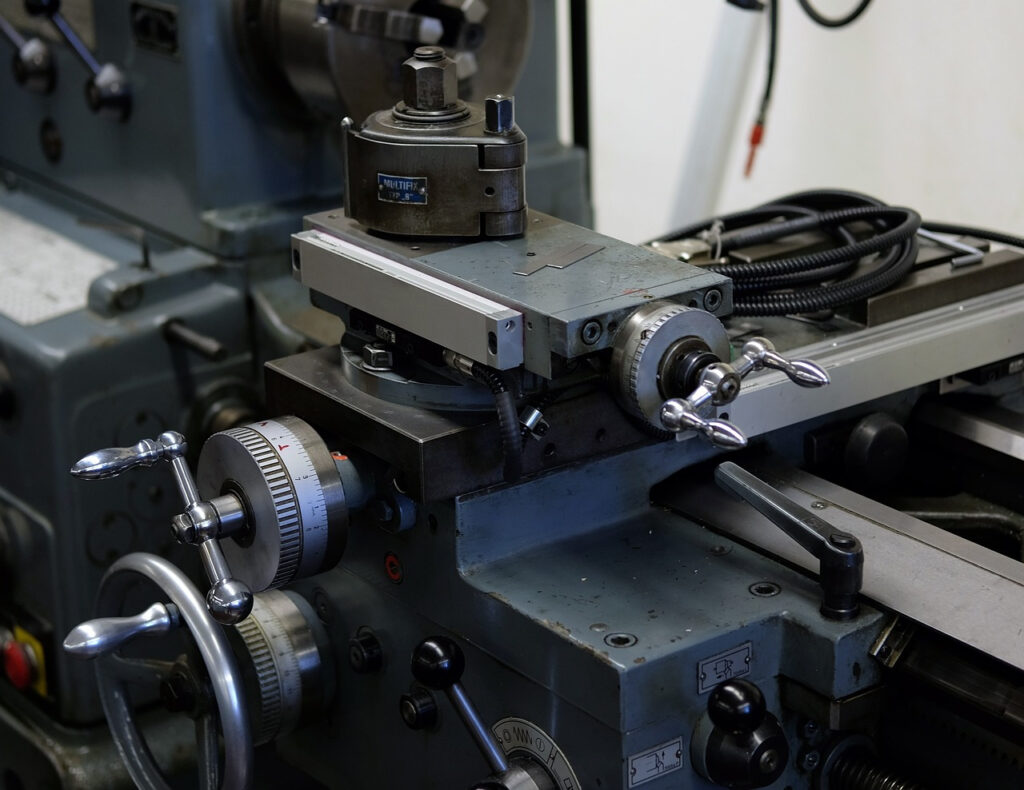
- 背景
数十年使用していた汎用旋盤だが、生産優先により日々の主軸のグリスアップを怠っていた。
汎用旋盤自体は皆で使う物なので、誰がメンテナンスするなど決めていなかった。
ある日旋盤を使おうと、主軸を回した所全然回らなくなった。
それどころか、ギーギーギーと主軸から異音が聞こえてきたので、急いで機械の使用を停止した。
皆、日常的にメンテナンスした事がないのでどこが壊れているのか分からなかった。
数日たってメーカ-に見てもらいグリスアップをしなかったのが原因でベアリングが故障したことが発覚した。
- 故障した原因
異音がしていたのは数か月前からあったのに誰も気にしなかった。
皆、汎用旋盤使っているのに誰もメンテナンスの関心がなかった。
使用している全員に聞きまわった所、主軸のグリスアップは数年間していない事が判明した。
- 対策
ル-ルを作り、汎用旋盤を使用する人達全員ローテ-ションで使用前にグリスアップするようにした。
機械メンテナンスの勉強会を開き、メンテナンスの重要性を周知徹底させた。
やらされてる感を出させないように、自分達で日常点検を作ってもらった。
- 結果
汎用旋盤にグリスアップをすることによって、その後、数十年間一度も故障することもなく、現在も現役で稼働中。
メンテナンスの意識が数十年間継承され、自分達で試行錯誤しながらルールの改定を繰り返しメンテナンス精度が高まった。
バイス取り付け前に実施したメンテナンス事例
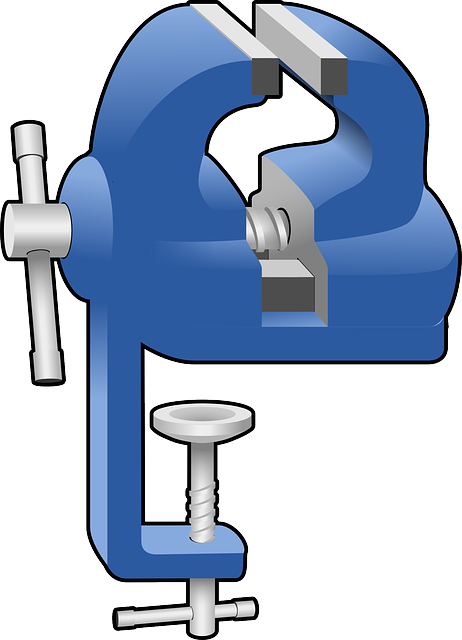
- 背景
汎用フライス盤でバイスに材料を取り付けて加工していた。
バイスの劣化が激しくて、移動ブロックが一定の場所に来るとハンドルが固くなっていた。
口金の材料設置面が長年使い込んだ影響で凹凸が激しいので寸法出しが出来ない。
よって荒削り用と位置付けていた。
・対策
バイスの部品を全て外して、サンドペーパーで全体的に錆びついている所を磨いた。
移動ブロックの締め付けネジをグリスアップした。
口金の凹凸が激しい所は、機械に取り付けてから削り直して平行を出した。
高所作業による怪我で安全意識の定着事例
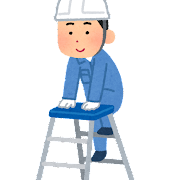
- 背景
工場内で地面から3m程高い所の蛍光灯を脚立を使って交換する作業を行っていた。
工場内の床は塗装したばかりで非常に滑りやすかった。
1人で交換作業をしていたので、脚立を支えてくれる人がいなかった。
脚立に上って交換作業中、脚立が滑り、足を踏み外して体が地面に叩きつけられ、足の骨が折れた。
・怪我した原因
工場内の床が塗装したてで滑りやすい。
脚立を支えてくれる人が周りにいなかった。
自身の作業を優先して手伝ってあげようとする人が誰もいなかった
・対策
高所作業のルールを作り、2人で作業するようにした。
助け合い精神が乏しかったので、似たような事故がないように安全最優先の事をグル-プ全体で周知した。
工場全体で安全意識を長い年月をかけて身に付けてもらった。
- 結果
高所作業のルールを作ってから、高所作業の怪我や事故がなくなった。
数十年の月日が立ち、初期グル-プメンバーが率先して助け合い行動をしているので、若手作業者も必然的に取るようになった。
安全意識が高いので、数十年間大きな事故、怪我がなくなった。
予防保全を定着した事で機械停止が低減した事例
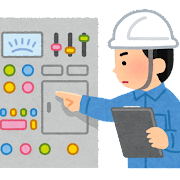
- 背景
ある日、工場内で機械の故障が相次ぎ発生し、生産に支障が出てしまった。
生産に影響出た為、納期が間に合わない事になり残業が増えてしまった。
古い機械もあるので故障に悩まされてしまう。
- 原因
日常点検を適当にやっていた。
作業者は故障するのは仕方がないという意識だった。
機械が動かなくなるまでに至るには予兆があるが、「動くからいいや」と気にしていなかった。
- 対策
日常点検を適当にやらないように定期的にチェックに回る。
故障は仕方ないという意識を無くすように機械担当者を設けて故障すると担当者が苦労する事を意識付ける。
機械の異変を感じたら上司に報告、緊急性があれば即対応して修理日程を立てる。
- 結果
日常点検を正確にやる事で、機械が停止してしまうような大きな故障が低減した。
機械担当者は故障しないように日頃から注意深く機械の状態を気にするようになった。
機械に異変があったら即報告するようになり、上司とコミュニケーションがスムーズに行われ、いきなり機械が故障する事が少なくなった。
予防保全が出来るようになろう
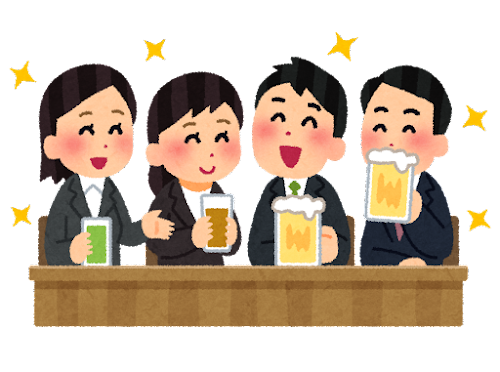
ここまでの成功例を上げましたが、やはり予防保全が一番大事な事です。
予防保全とは、機械が故障しないように、日頃から機械のメンテナンスを面倒がらずに行うことです。
これから益々機械化が進んでいきます。
機械は自分でメンテナンス出来ない以上、人がやるしかありません。
機械の状態を常に監視して、残業が少なくなるようにプライベートの時間を沢山作りましょう。
コメント