この記事は3分位で読み終えます。
歩留まり(ぶどまり)と言う言葉をご存じでしょうか。
実は現場改善では欠かせないとても重要な指標です。
一から調べるのは大変ですが、本記事から歩留まり率を知り、改善活動に活かして頂けたら幸いです。
歩留まりの良し悪しは直接利益率に直結するので、知っていると現場改善に大きく貢献しますよ。
分かりやすく説明すると
・原材料から完成品になってどれだけ削って廃棄したか
・不良品をどれだけ作ってしまったか
どうでしょうか?直接的に現場に関わる事柄ですよね。
この記事は歩留まりの計算方法と改善の仕方を分かりやすく紹介する記事になります。
是非最後までチェックして現場改善に役に立てて下さい。
歩留まりとは?
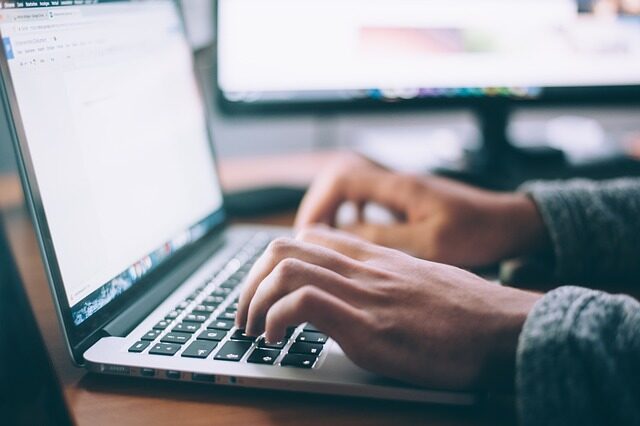
歩留まりあるいは歩止まり(ぶどまり)とは、製造など生産全般において、「原料(素材)の投入量から期待される生産量に対して、実際に得られた製品生産数(量)比率」のこと
機械加工現場において原材料から完成品の割合をパーセンテージで表し、歩留まり率として使って行きます。
歩留まり率が良いと次のように判断出来ます。
歩留まり率が良い
- 不良品、手直し品が少ない
- 原材料から廃棄される切りくずが少ない
簡単に言ってしまえば、不良が少なく、廃棄も少ないムダがない作業現場ってことになります。
歩留まり率は現場に寄り添った指標なので機械加工現場ではかなり役に立つでしょう。
歩留まりの計算方法
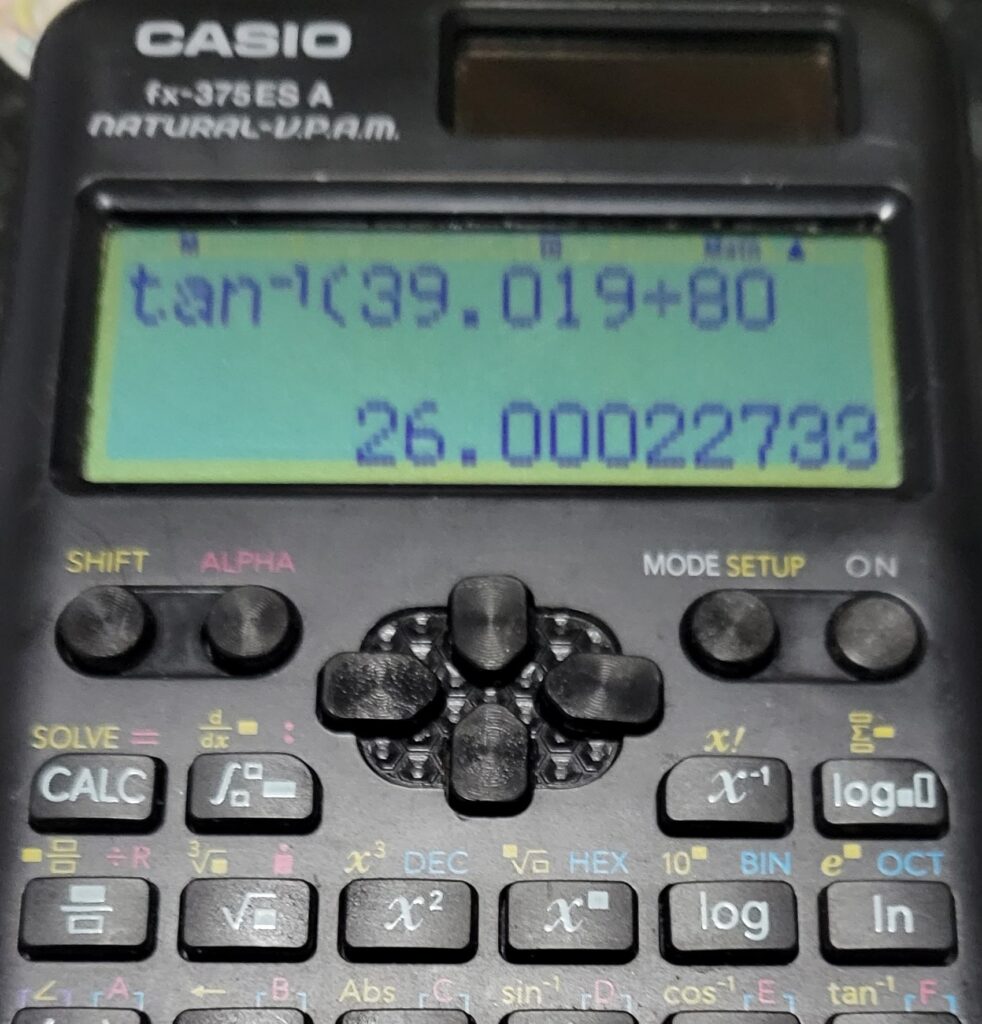
歩留まりの計算式は以下の通りです。
【生産数の歩留まり率】歩留まり率(%)=良品数÷総生産数×100
【原材料に対する歩留まり率】歩留まり率(%)=完成品の重さ÷原材料の重さ×100
例えば生産数の歩留まり率は100個の良品数を作る上で総生産数は120個とすると歩留まり率は約83%になります。
歩留まりの重要性
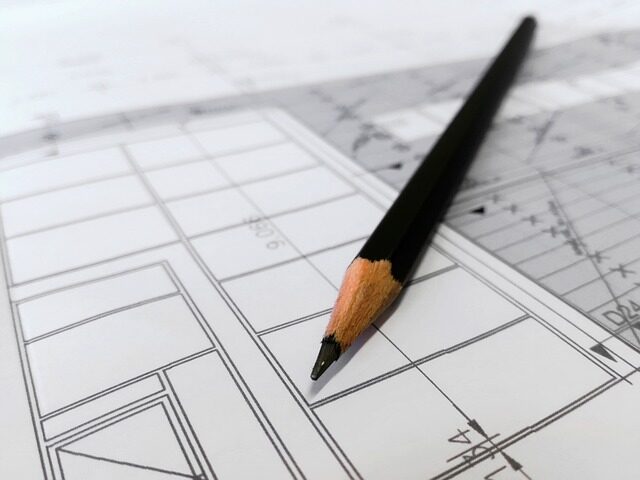
歩留まり率で生産管理を行うと、現場で何が問題になっているか分かります。
- コスト削減:不良が少なくなることで材料を無駄がなくコストが削減されます。
- 効率的な生産:歩留まりが高いと生産効率が上がり、納期も短くなります。
- 環境への配慮:材料の無駄を減らすことで環境負荷も軽減されます。
歩留まり率が高いと不良が少なく、原材料から切削して出る切りくずの量も少なくてムダがない生産をしている事になります。
直接的な利益に結び付くので歩留まりは重要な指標です。
歩留まり率以外で合わせて把握するもの
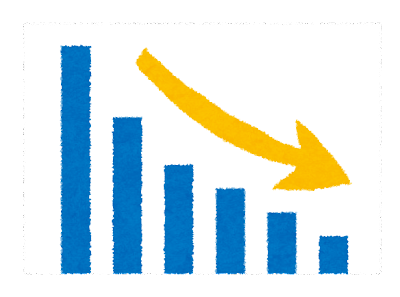
歩留まり率を考える時には合わせて把握しておいた方が良い指標があります。
- 不良率:生産時に出た出荷出来ない不良品の割合
- 手直し率:出荷出来ない不良品を手直して良品にした割合
- 転用率:不良品を他の製品に転用できた割合
- 廃棄率:手直しも転用も出来ない不良品の割合
- 良品率:手直し品も含めて最終的に良品になった割合
- 直行率:1度生産工程で良品になった割合
以上の事を歩留まり率と平行して考えると現場に何処が問題になっているか分かります。
その際は4Mで考えると良いでしょう。
4Mとは
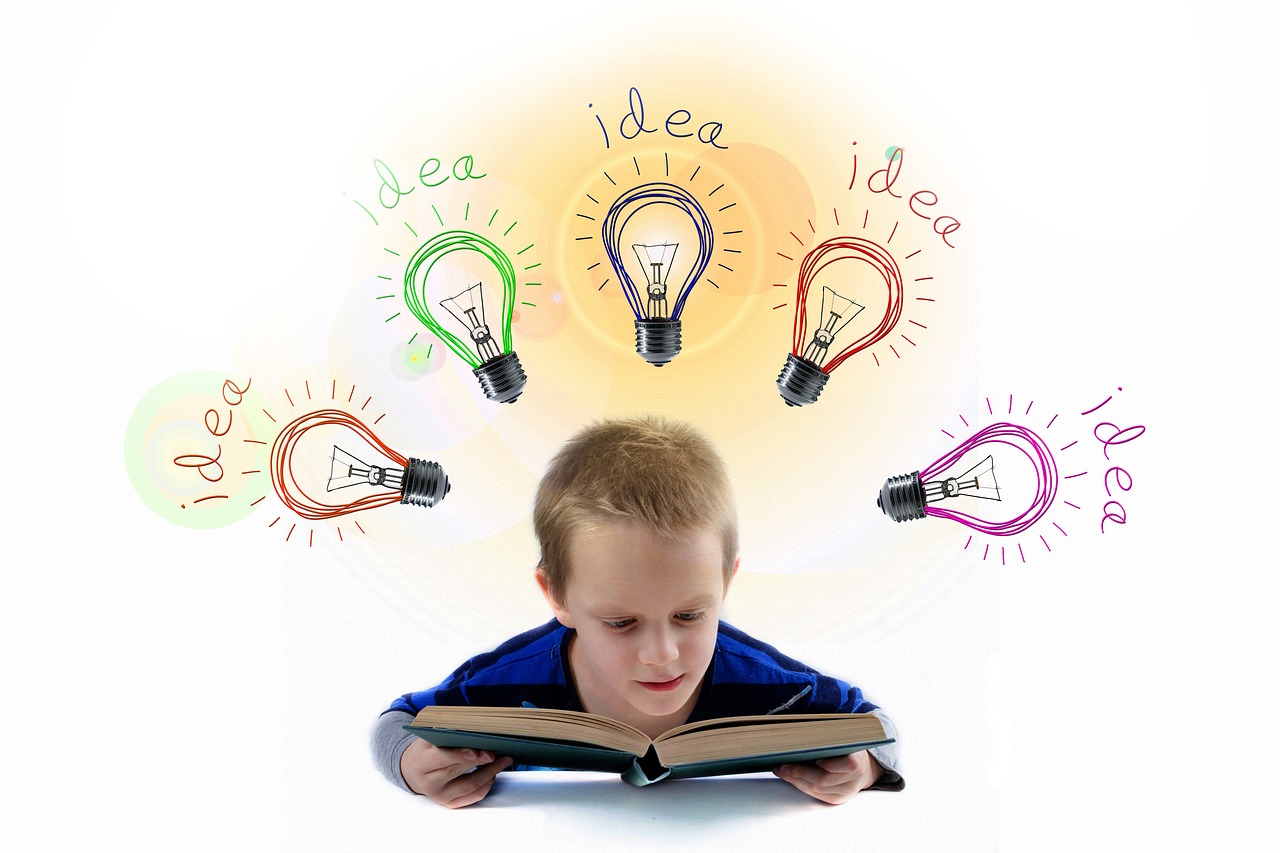
4Mとは頭文字のMを取った現場の問題解決や課題発見に役に立つフレームワークの一つです。
4Mとは
- Man:人
- Machine:機械
- Material:材料
- Method:方法
僕の経験上、歩留まり率が悪い問題はほとんど4Mの何処かに該当します。
それでは実際に4Mで問題解決した一例を紹介します。
あなたの現場に置き換えて考えて頂くとより一層分かりやすいでしょう。
4M:人の問題点(MAN)
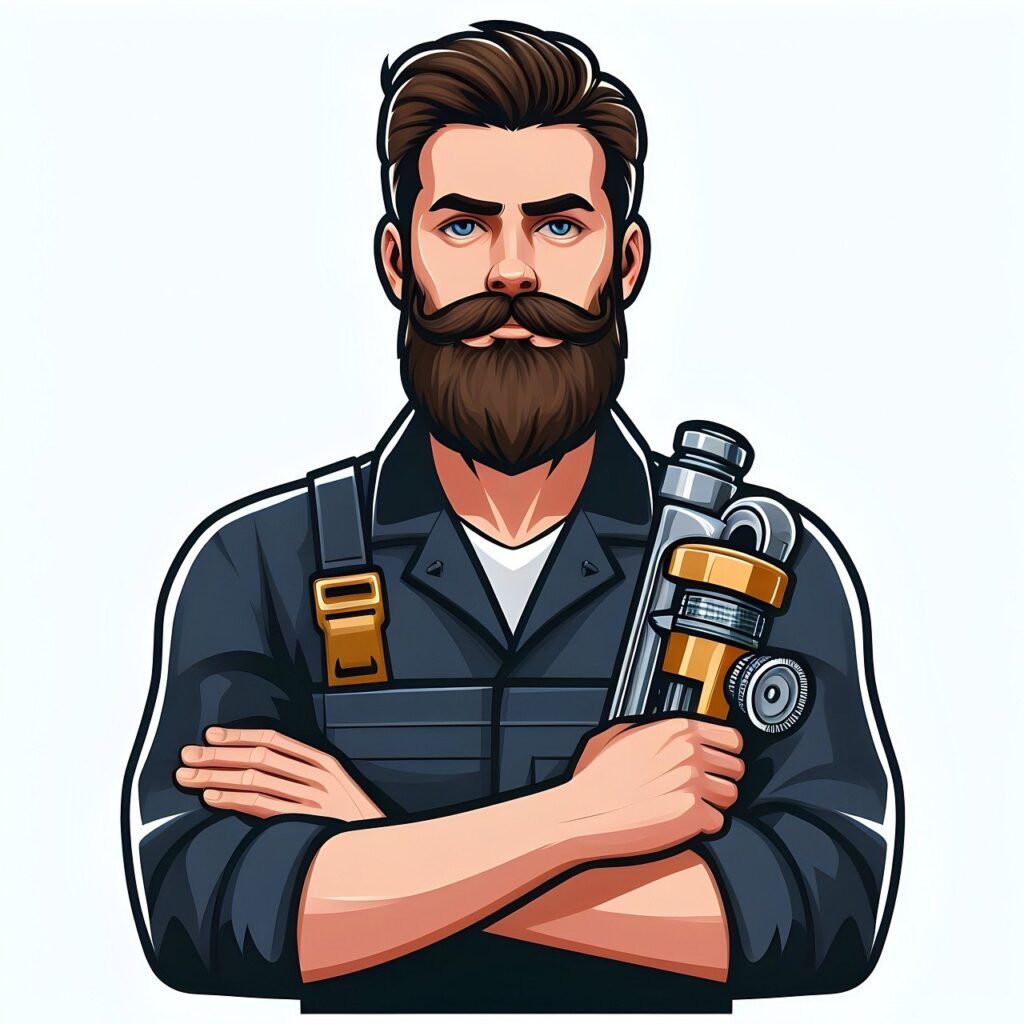
問題点 | 説明 | 例 |
---|---|---|
技術力 | 作業者の技術的な能力 | 未熟な作業者による加工ミス |
経験 | 作業者の実務経験 | 新人作業員によるトラブル発生 |
訓練 | 作業者への教育訓練状況 | 訓練不足による操作ミス |
モチベーション | 作業者のやる気や意欲 | モチベーション低下による効率低下 |
人間はロボットではなので、多からず少なからずミスをしてしまいます。
上記の問題点を現場監督者の方は作業員1人1人知っておかなければならないでしょう。
機械操作は人間が行うため、歩留まり率に大きく関わるのは大体人の問題が多いと思います。
その中でも、機械操作の知識が乏しかったり、モチベ-ションを下げるような事が起きれば不良品が多くなるし、生産効率も下がります。
解決方法
問題 | 解決方法 |
---|---|
技術力の不足 | 技術者による教育の実施 |
経験不足 | ベテラン作業者とペア作業、メンター制度の導入 |
訓練不足 | ベテラン作業者とOJT、資格取得の推奨 |
モチベーション低下 | インセンティブ制度の導入、職場環境の改善 |
聞いたことがない言葉もあるかと思われるため、僕の効果的だった解決方法を含めて解説します。
- メンター制度とは、仕事で先輩(メンター)が、後輩(メンティー)を支援する制度であり、先輩が自分が経験した事や失敗談を後輩に話し、同じ過ちを繰り返さないようにさせるのが一番効果的です。
- OJTとは「On-the-Job Training」の略で、現場で実務を行いながらベテラン作業者が作業者を即戦力として育てる人材教育方法であり、ある程度技術がある作業者なら問題ありませんが、未経験者だと基礎的な事が分からなくなる可能性があります。効果的に実施するには、基礎的な所から始めましょう。
- インセンティブ制度とは、従業員の目標達成や業績に応じて金銭的な報酬や表彰、昇進などの形で報酬を与える制度であり、現場監督者が皆の前で褒めてあげるだけでも効果テキメンです。
以上のように人の問題を解決し歩留まり率向上に努めましょう。
4M:機械の問題点(Machine)
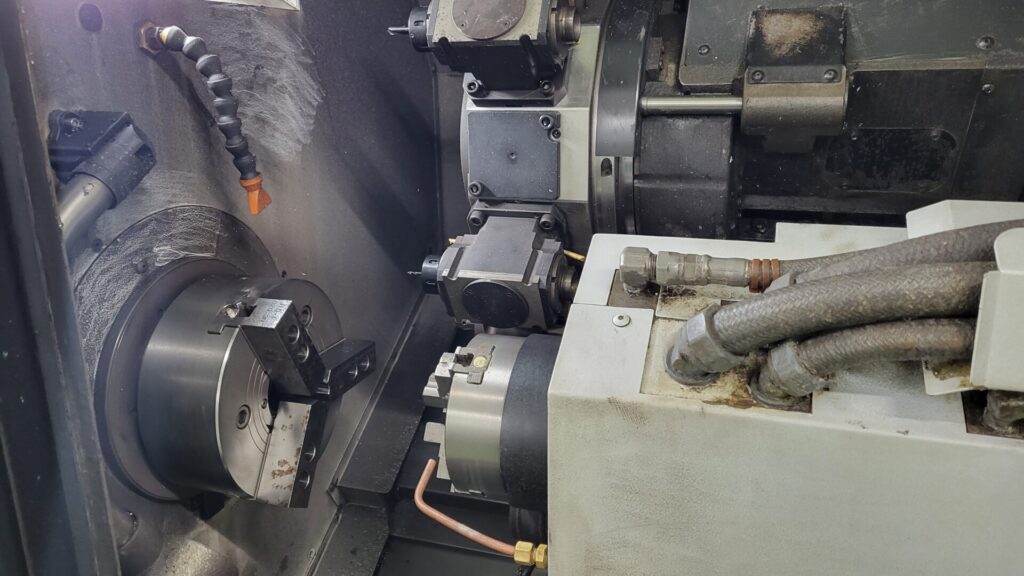
要因 | 説明 | 例 |
---|---|---|
機械性能 | 機械の能力や機能 | 機械スペック不足 |
機械精度 | 機械の加工精度 | 古い機械などによる品質低下 |
メンテナンス | 機械の保守・点検状況 | メンテナンス不足による故障 |
設置環境 | 機械の設置条件や環境 | 振動や温度変化による影響 |
機械は製品を大量生産してくれる便利なものですが、道具の1つにすぎません。
目的以外の性能は発揮しないし、使い続けていれば機械精度は年々落ちてきます。
長く使い続けるため日々のメンテナンスと機械設置前に振動に耐えうる工場内の地盤基礎工事も必要です。
又、機械加工の仕事に至っては、μ(ミクロン)単位で寸法管理しているため、温度変化に弱く室内温度を一定にする必要があります。
以上の事を僕の経験した解決方法を紹介します。
解決方法
問題 | 解決方法 |
---|---|
性能不足 | 最新機械への更新、必要な機能の追加 |
精度不足 | 精度の高い機械の導入、定期的な精度確認 |
メンテナンス不足 | 毎日の機械使用前点検、 |
設置環境不良 | 温度管理の徹底、振動対策を行う。 |
僕が実際に現場で効果的だった解決方法です。
もっと分かりやすいようにまとめました。
- 機械のスペックを取り扱い説明書もしくは機械メ-カ-に確認し、機械の最大機能に対して、7割程度と割り切り余力を残しておく。足りなければ、最新設備の導入、もしくは設備に機能オプション追加
- 定期的に機械に衝撃を与えてしまった事を除き、1か月に1回程度機械精度確認。又古い機械はどうしても制度が悪くなりがちなので妥協点を決め、設備更新を視野に入れてもらう。
- 毎日日常点検を行って大きな故障になる前に早期発見する。
- 可能であれば空調管理できる環境にする、又機械設置個所が大きな振動に対応できる基礎地盤にする。
余力を残しておくのはメーカ-は一番良いデータが取れたチャンピオンデータで話す傾向があるからです。
なぜなら、現場では毎日作業するため機械トラブルが発生したり、人的ミスがあったりしてチャンピオンデータと同じように加工できるとは考えにくいからです。
新規設備導入の際は営業トークに惑わされないようにして下さい。
4M:材料の問題点(Material)

要因 | 説明 | 例 |
---|---|---|
品質の悪化 | 材料や部品の品質 | 不良の材料を使用 |
材料の供給状況 | 材料の供給が安定しているか | 材料の納期が遅れる |
材料の保管 | 材料の保管方法 | 誤った保管方法による材料の劣化 |
ロット管理 | 材料をロットごとの管理 | ロット間の品質ばらつき |
現場で良くありがちなのは「ちょっとくらいの不良材料は使えてしまえば問題ない」って発想です。
あなたが気が付いても他の人が気が付かなければ不良品を作ってしまう可能性があります。
そうなると歩留まり率を下げる要因になりかねませんので注意が必要です。
解決方法
問題 | 解決方法 |
---|---|
材料の品質ばらつき | 仕入れ先の品質管理強化、受け入れ検査の徹底 |
材料供給状況の不安定 | 代替仕入れ先の確保、在庫管理の徹底 |
材料保管方法の不適切 | 適切な保管環境の整備、定期的に材料をチェック |
ロット管理の不備 | ロットごとに追跡調査を強化、品質管理システムの導入 |
材料を購入に対して外注に依頼しているのであれば、受け入れ検査は必須事項です。
分かりやすくまとめました。
- 現場の人はちょっとでも不良材料と判断したら、上長に報告し判断を仰ぐ。使えてしまうから大丈夫的な発想は会社側、材料メーカ-共によろしくない。
- 材料メ-カ-は1社に絞らず、代替仕入れ先を確保する。客先の納期対応を最優先に考え、代替仕入れ先は金額ベースに折り合いつかなくても付き合いしていくのが良い。
- 問題が発生した時に備えてトレーサビリティ(追跡調査)が出来るように品質管理システムを導入
材料の問題は外注先が絡んでくるので解決するのはなかなか難しい問題です。
外注先が取引しませんと言われない範囲内で立ち回るしかなく折り合いつけるにはコミュニケーション能力が問われます。
それには品質管理システムがあると交渉する時にとても便利です。
材料の問題が解決すれば生産活動がスム-ズになるので、解決出来れば歩留まり率は大幅に改善されるでしょう。
4M:方法の問題点(Method)
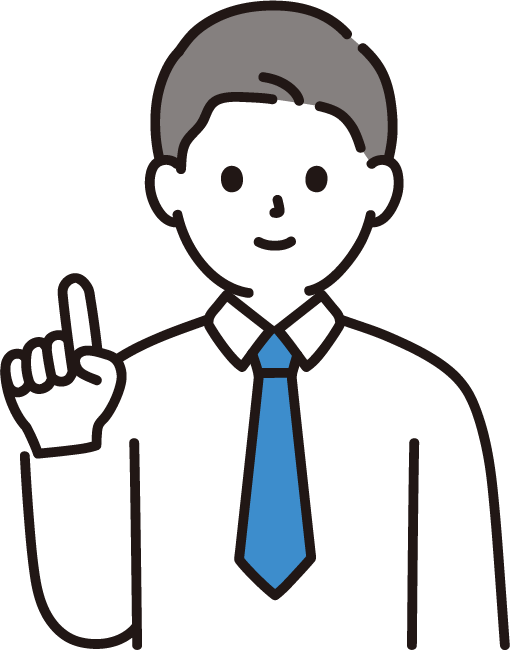
要因 | 説明 | 例 |
---|---|---|
作業手順 | 作業の具体的な手順 | 手順書の不備 |
標準化 | 手順の標準化の状況 | 標準化されていない作業 |
作業環境 | 作業が行われる環境 | 照明不足や作業スペースの問題 |
改善状況 | 手順や方法の改善状況 | 改善が反映されていない手順 |
僕が若い時は「機械加工の仕事は目で盗め」みたいな事を職人気質の昭和世代の人に言われましたが、今の世代にそのような対応したらハラスメント扱いにさせてしまいます。
大きな飲食チェ-ン店などではアルバイトに教育する為に分かりやすく写真付きの作業標準書があります。
また、作業1つ取っても秒単位で標準化されており、アルバイトの入れ替わりの激しい業界上短期間で即戦力になってもらえる体制にしているようです。
機械加工の現場も同じように考えればいいのです。
解決方法
問題 | 解決方法 |
---|---|
手順書の不備 | 手順書の見直しと更新、作業手順の標準化 |
標準化されていない作業 | 作業手順の標準化、定期的な手順書の見直し |
作業環境の問題 | 作業環境の改善(照明、作業スペースの確保など) |
改善が反映されていない手順 | 改善案の迅速な反映、定期的な手順の見直し |
作業手順書、作業標準書の作成は写真付きでもいいのですが、タブレット等で動画撮影するのもおすすめです。
要は相手に分かりやすく伝える方法なら何でも良いと思います。
相手に分かりやすく伝えるのって大変なんですよね。
作業スぺ-スの確保や照明など日頃から整理整頓するクセを身に付けて置くと改善の糸口が見つけやすいです。
まとめると
- 作業手順書や作業標準書は分かりやすいように写真付きが良い(動画撮影も可)
- 改善は日頃から整理整頓するクセをつけておくと案が出やすい
- 改善に終わりはないので、作業手順書の更新は忘れずに
4Mから導き出した答えから歩留まり率を上げよう
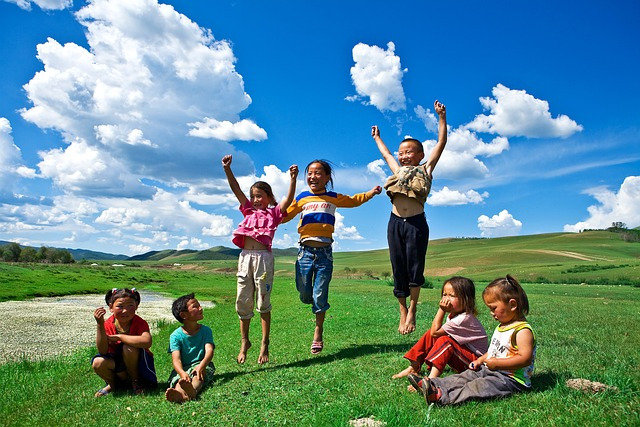
今回はどちらかと言うと管理者側からの視点からみた記事になりますが、一般社員の方でも歩留まり率の事を知っていると将来的に役に立つ事が多いでしょう。
歩留まり率を知っているか知っていないかで当てずっぽうで改善を行うより、4Mから導き出された答えから改善活動に挑んだ方が結果がでるのは皆無です。
最後まで読んで頂きありがとうございました。
コメント